You are here: Home1 / iTestSystem Blog2 / Blog Posts3 / Aerospace | Defense4 / High Channel Count Synchronous Datalogging
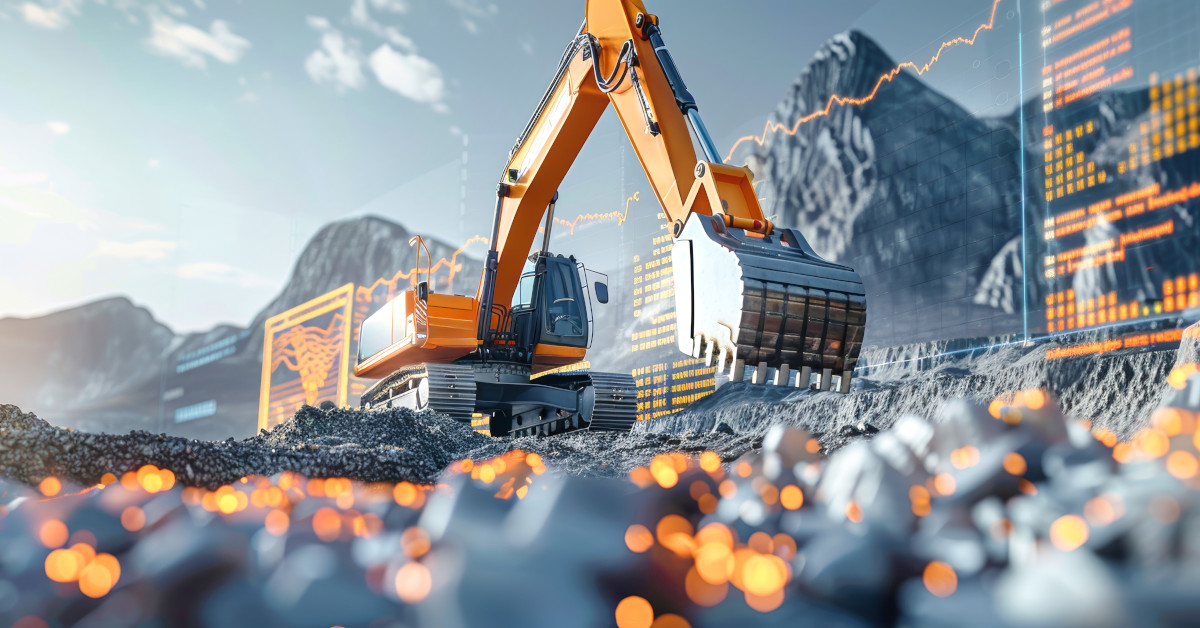
Author: Ryan Welker – Integrated Test & Measurement (ITM), LLC
Industry: Heavy machinery/Construction/Mining
Keywords: High-Channel Count, Synchronous Datalogging, iTestSystem Automated Analytics, iTestSystem Notification Service, AWS IoT, Condition-Based Monitoring, Digital Twin, Design Validation, Customer Usage Profiling
NI Products Used: iTestSystem, NI cDAQ-9189, NI 9236, NI cDAQ-9188, NI 9469
High-Channel Count Synchronous Datalogging – Now Extended to Edge-to-Cloud Insights
Executive Summary
When a manufacturer needed to validate the structural performance of a 38-ton on-highway vehicle, ITM deployed a 200+ channel synchronous datalogging system capable of capturing accelerometer, strain, GPS, and speed data at nearly 2 kS/s per channel across multiple NI cDAQ chassis.
Originally designed to provide engineers with terabytes of high-fidelity time-aligned data for design validation, the system now goes further: iTestSystem’s Automated Analytics process key metrics at the edge and publish them via iTestSystem Notification Service to the AWS cloud, allowing operators and reliability teams to evaluate usage patterns and structural health in real time.
The Challenge
The customer required accurate structural data to validate a high-value design and to gain confidence in fatigue life predictions. To achieve this, engineers needed to synchronously collect hundreds of channels without sacrificing data quality or requiring repeat tests.
But another challenge loomed: operators and decision makers wanted faster insight than traditional offline analysis could deliver, along with a way to scale usage analytics across fleets and test sites.
The Solution
Synchronized Edge Acquisition + iTestSystem Automated Analytics + Cloud Notification Service
Multi-Chassis Synchronous DAQ
- ITM deployed six networked NI cDAQ chassis, synchronized via NI-9469 modules, to record 200+ channels of accelerometer, strain, GPS, and speed data.
- Managed through iTestSystem and its MultiDAQ plug-in, engineers achieved perfect channel alignment across all sources.
Automated Edge Analytics
- Using iTestSystem Automated Analytics, the system performed real-time calculations of RMS, peak, kurtosis, rainflow cycle counting, fatigue damage indices, and duty cycle metrics.
- These analytics condensed terabytes of raw waveforms into decision-ready KPIs without delaying test operations.
Edge-to-Cloud Communication
- Summarized KPIs were streamed securely to the AWS cloud using iTestSystem Notification Service, which handles message formatting, compression, and delivery over MQTT/HTTPS.
- Raw datasets were still retained locally, while the cloud received usage KPIs and event-driven alerts for scalable visualization and fleet comparisons.
Cloud Visualization & Workflow
- In AWS, data landed in IoT Core, Timestream, and S3, supporting dashboards in Grafana and QuickSight.
- Notifications also triggered workflows via EventBridge, alerting operators when fatigue thresholds or anomaly conditions were detected.
Results
High-Fidelity Data Confidence
- Engineers collected ~20 GB of data over 10 days, covering the full range of operating conditions without reruns.
- The synchronized dataset enabled true modal analysis, usage profiling, and structural validation.
Actionable Insights in Near Real Time
- Operators accessed dashboards showing vibration KPIs, load spectra, and fatigue usage metrics, instead of waiting for offline reports.
Data Efficiency
- Automated Analytics reduced transmission bandwidth by 10–100×, ensuring cloud data was lean but still linked to underlying raw records.
Fleet-Wide Intelligence
- Through iTestSystem Notification Service, the architecture now supports multi-asset monitoring, trending, and usage-based maintenance decisions.
Edge-to-Cloud Architecture
- Sensors – Strain gauges, accelerometers, tach, GPS
- DAQ Layer – Multi-chassis NI cDAQ synchronized via NI-9469, controlled by iTestSystem MultiDAQ
- Automated Edge Analytics – iTestSystem computes KPIs in real time (RMS, fatigue indices, rainflow cycles, anomalies)
- Notification to Cloud – iTestSystem Notification publishes KPIs and alerts to AWS IoT Core
- Cloud Services – Timestream (time-series KPIs), S3 (raw data), EventBridge (alerts)
- Dashboards – Grafana & QuickSight deliver operator and engineer views
Conclusions
The original case study demonstrated that ITM could deliver synchronous, high-channel data acquisition for structural validation at scale. With the addition of iTestSystem’s Automated Analytics and Notification, ITM now bridges the gap between edge data acquisition and cloud intelligence.
Engineers retain access to the complete high-rate dataset for design validation, while operators gain immediate visibility into usage, fatigue, and health KPIs through AWS dashboards—enabling condition-based maintenance, faster design decisions, and scalable fleet monitoring.
Author Information: For more information about this Case Study, our Testing Services or iTestSystem (our data logging application) contact: Ryan Welker‐ Integrated Test & Measurement (ITM), LLC – ryan.welker@itestsystem.com
Share this entry
RelatedLinks:
Predictive Maintenance and Structural Monitoring with Sensors
CONTACT INFORMATION
ITM | Integrated Test + Measurement
227 Water Street, Suite 300
Milford, OH 45150
Phone: 1.844.TestSys
Fax: 513.248.8453
Email: ITM Sales
ITM provides software development, structural and mechanical testing services, industrial monitoring, strain gauging, and data analysis solutions to clients on six continents. ITM is a recognized National Instruments Gold Alliance Partner.