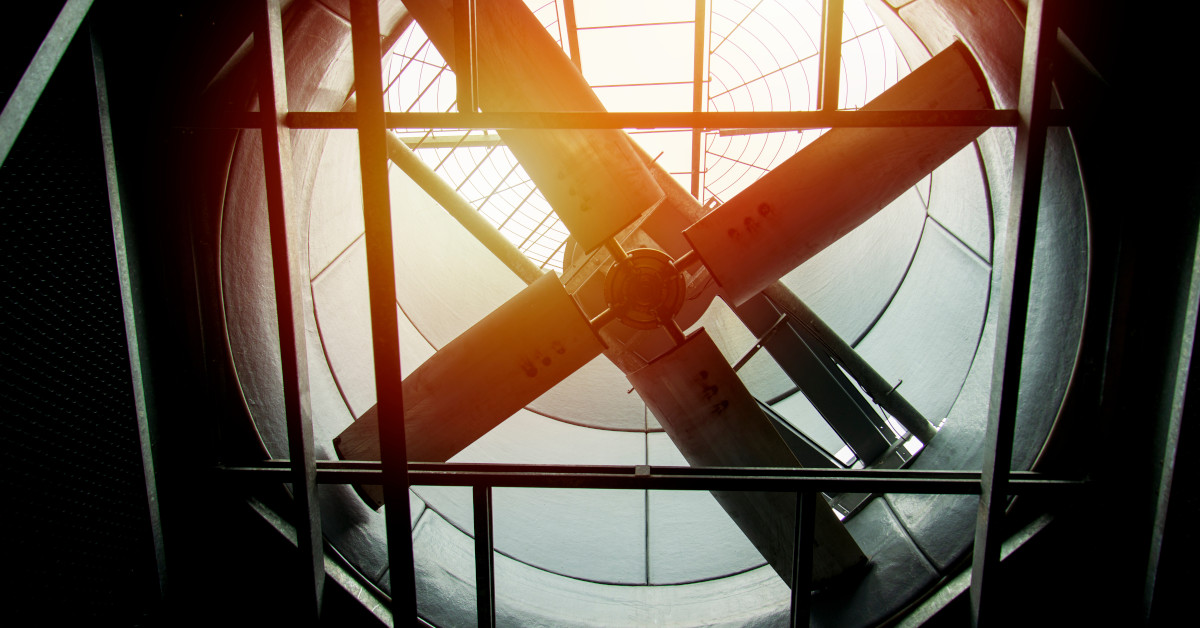
Cooling tower fan blades with strain-based transducers.
Strain Gauges Improve Cooling Tower Fan Performance
Cooling towers are an integral part of geothermal power plants, as they help to cool the water used in the power generation process by circulating air using large fan blades.
However, the fan blades of cooling towers are subjected to high levels of stress and vibration, which can result in damage and failure over time. Hence, regular inspection and testing of these fan blades are crucial to avoid potential issues that could lead to costly downtime.
Test Case: Philippines Cooling Tower
In a recent case, Integrated Test & Measurement (ITM), a leading engineering solutions provider, was called upon to perform strain gauge testing on a composite cooling tower fan blade at a geothermal power plant located in Mount Apo, Philippines.
The goal of the testing was to measure the stresses on the fan blade and identify any potential issues before they resulted in costly downtime. Our team took a detailed approach to the task, and our methodology can serve as a blueprint for inspecting and testing fan blades in power plants.
The first step of the process was a thorough inspection of the fan blade and its surrounding structure. We identified key locations on the fan blade where stresses were likely to be highest and installed strain gauges at these points. The team also installed accelerometers to measure the vibration of the fan blade during operation.
Strain gauges are sensors that measure the strain or deformation of an object, while accelerometers measure the acceleration or vibration of an object. By installing these sensors, the ITM team was able to gather data on the performance of the fan blade during normal operation and during extreme wind conditions.
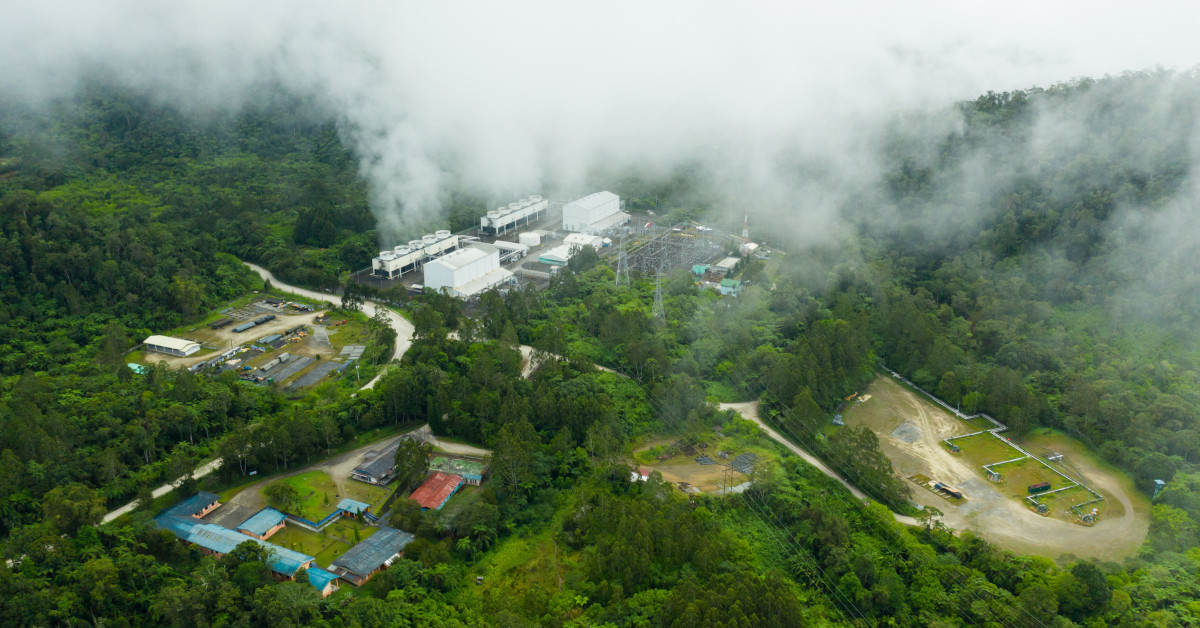
Geothermal Plant at Mount Apo, Philippines
After collecting the necessary data, we analyzed it to identify any issues with the fan blade’s performance, such as excessive stress or vibration. The team discovered that the fan blade was experiencing high levels of stress at the root of the blade, likely caused by an imbalance in the blade. They also found that the fan blade’s vibration was higher than expected, indicating a problem with the bearings or the blade’s balance.
Based on this analysis, we recommended that the fan blade be balanced and that the bearings be inspected and replaced if necessary. Additionally, the team suggested reinforcing the fan blade’s root to distribute the stresses throughout the blade more evenly. Our team worked closely with the power plant’s maintenance team to implement these changes and perform follow-up testing to ensure that the fan blade was operating within the desired specifications.
Our attention to detail and comprehensive testing procedures allowed us to identify potential issues with the fan blade before they led to costly downtime. By utilizing strain gauges and accelerometers to measure the performance of the fan blade, the team was able to pinpoint specific areas of concern and make targeted recommendations to improve the blade’s performance. The collaboration with the power plant’s maintenance team ensured that the necessary changes were made promptly, and the follow-up testing confirmed that the fan blade was operating optimally.
Overall, this is a prime example of how ITM can assist in improving the performance and reliability of equipment in power plants. By leveraging our expertise and advanced testing methods, we can help power plants to identify potential issues and make informed decisions to prevent costly downtime.
Additionally, ITM’s involvement in this project highlights the importance of regular inspection and testing of equipment in power plants, as these proactive measures can help to avoid costly repairs and downtime in the long run.
To review, cooling tower fan blades are essential components in geothermal power plants, and their performance must be regularly monitored to ensure the optimal operation of the plant.
ITM’s use of strain gauges and accelerometers to measure the performance of the fan blade allowed us to identify potential issues and make targeted recommendations to improve its performance. By working closely with the power plant’s maintenance team, we were able to implement the necessary changes promptly, which helped to avoid costly downtime.
Why turn to ITM for Strain Gauge expertise?
Integrated Test & Measurement (ITM) is a leader in the field of designing and manufacturing strain gauge based transducer technology for various industries. Over the years, the company has gained extensive experience in using this technology to perform measurements on a wide range of equipment, from wind turbines to aircraft engines.
Strain gauges are a type of sensor that measure the amount of strain, or deformation, that occurs in a structure when it is subjected to a load. The deformation is then converted into an electrical signal that can be analyzed to provide valuable information about the behavior of the structure.
ITM has successfully used strain gauge technology to perform a variety of tests, including strain testing, force measurement, torque measurement, and pressure measurement. These tests can help to identify issues such as stress concentrations, overloading, and fatigue in a wide range of components and systems.
One of the key advantages of strain gauge technology is its ability to provide accurate and reliable data in real-time. This allows engineers and technicians to quickly identify potential problems and take corrective action before they result in costly downtime or equipment failure.
ITM has also developed advanced software and data acquisition systems that allow for efficient and comprehensive data collection and analysis. This technology enables the company to provide clients with detailed reports and recommendations based on the results of their testing.
Overall, ITM’s experience with strain gauge based transducer technology has allowed the company to provide valuable insights and solutions for a wide range of industries, helping to improve the performance, safety, and reliability of various types of equipment.
Our team specializes in stress testing, preventative maintenance, equipment reliability, downtime reduction, composite materials, stress distribution, equipment testing, real-time data, pressure reading, reducing unplanned downtime, strain gage, gauge pressure, regular maintenance, manufacturing plant, electrical resistance, pressure ranges, planned downtime turn the fan, downtime event, absolute pressure sensor, static pressure, pressure application, increases productivity, wheatstone bridge and much more.
Contact us to learn more about this project or to connect with our team on your own strain gauge, data acquisition or engineering challenges?