How to Validate your next Finite Element Analysis (FEA) Model using Strain Gauges
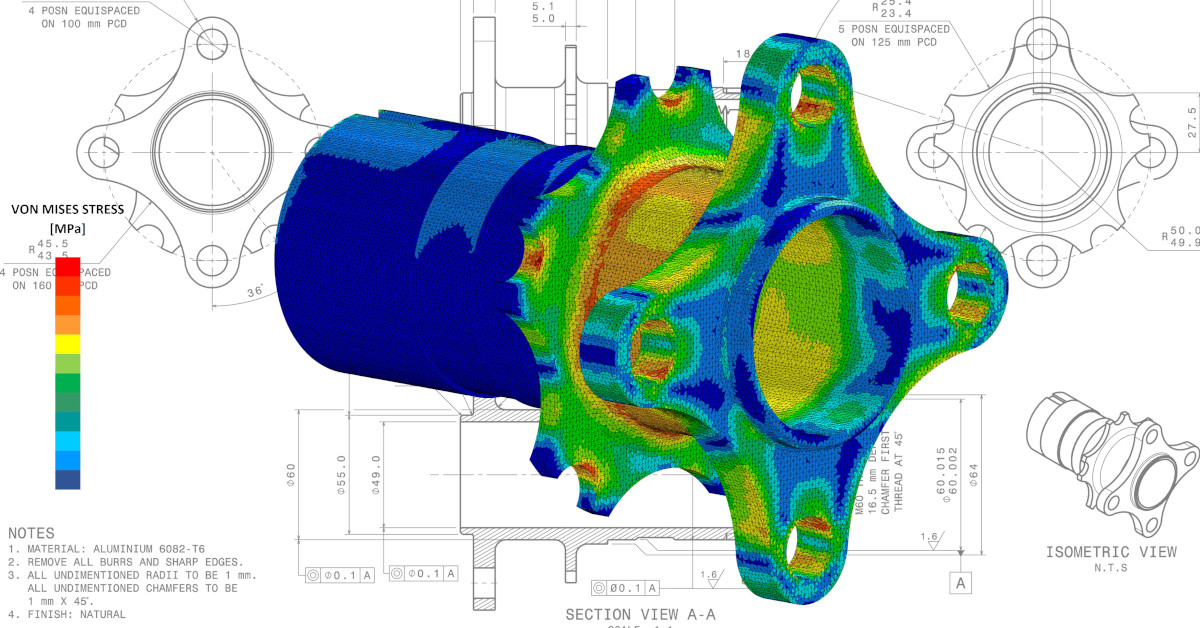
Car Suspension Hub FEA Model from Strain Data
Finite Element Analysis (FEA) is an indispensable tool in the realm of engineering, providing insights into structural behaviors under various conditions. But as with any computational model, its results are only as reliable as the underlying assumptions and the quality of input data. That’s where validation becomes crucial. One of the most reliable methods of validating FEA models in practice is by using strain gauges. Here’s how strain gauges can be used to validate the FEA model:
- Instrumentation: Strain gauges are attached to the actual physical component in locations corresponding to areas of interest on the FEA model. Typically, these are areas where high stresses or strains are predicted, such as those highlighted in the model’s warmer colors (red and orange zones).
- Data Collection: The physical component is then subjected to real-world loading conditions, which replicate or closely resemble the conditions modeled in the FEA analysis. As the component undergoes these loads, the strain gauges measure the resulting strains in real-time.
- Correlation with FEA Predictions: The measured strain values from the gauges are then compared to the strains predicted by the FEA model. This direct comparison helps validate whether the model’s predictions closely align with the real-world behavior of the component.
- Analysis Refinement: If discrepancies exist between the real-world data and FEA predictions, the model can be adjusted or refined based on the strain gauge data. This iterative process ensures that the FEA model becomes more accurate and representative of the actual behavior of the component.
- Focus on Critical Points: The FEA model often highlights critical points, like areas with maximum stress or potential weak points. Validating these specific points with strain gauges ensures that the model accurately predicts the behavior of the most critical parts of the component.
- Capture Non-linear Behavior: While FEA can capture and predict non-linear material behavior, validating these predictions with real-world data from strain gauges ensures the material model used in the FEA is accurate. This is particularly important in areas that might experience plastic deformation or undergo stress concentrations beyond the material’s elastic limit.
- Confirmation of Assumptions: FEA models rely on a number of assumptions regarding boundary conditions, material properties, and load application. Strain gauge data can provide insights into the accuracy of these assumptions and can be invaluable when trying to diagnose discrepancies between the FEA predictions and actual test results.
In essence, strain gauge testing provides a bridge between theoretical predictions from FEA models and real-world behavior of components. It’s a vital step in the engineering design and validation process, ensuring that the final designs are both safe and optimized for their intended applications.
Contact (Contact Us | ITM (itestsystem.com)) an ITM Engineer to begin the process.