Push Your Motorsports Team to the Limit with ITM’s Rod End Load Cell Expertise
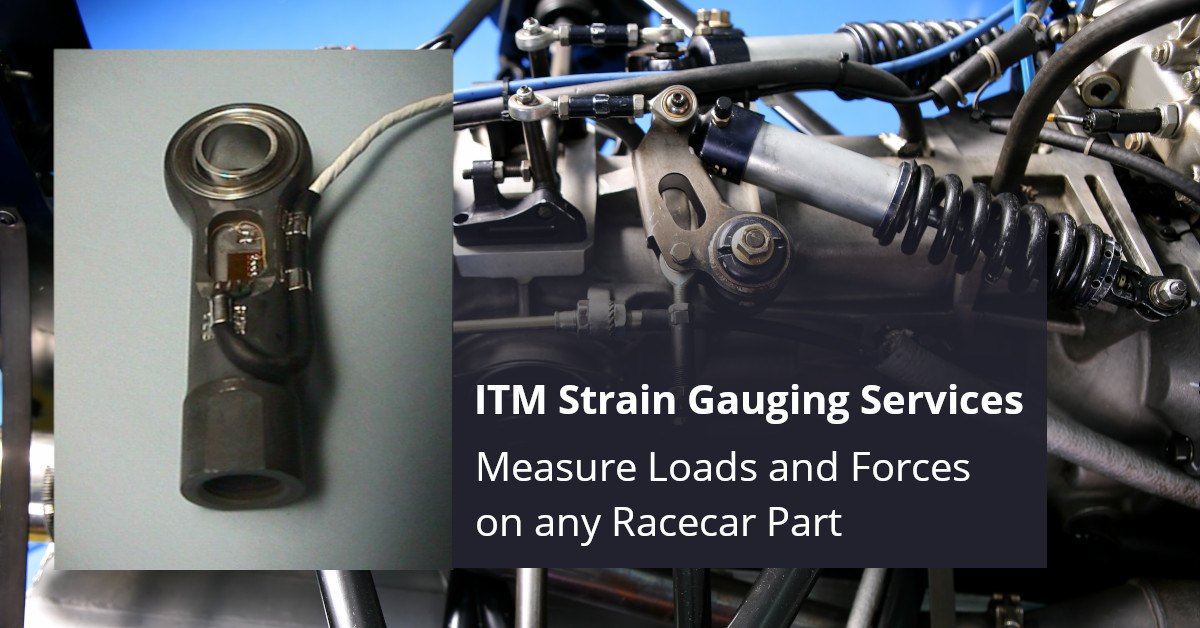
Strain Gauge installed on a Shock Eyelet which is Overlayed on a Formula One race car.
Turn our strain and torque load cell experts loose to gain performance on your test track
At ITM, your race car’s exact load and downforce can be precisely measured using rod end load cell and torque load cell technology.
Putting our strain gauging expertise to work allows race teams from NASCAR, Formula 1, IndyCar and others to modify designs, decrease stress and gain a competitive advantage.
Putting our strain gauging expertise to work allows race teams from NASCAR, Formula 1, IndyCar and others to modify designs, decrease stress and gain a competitive advantage.
A strain gauge, or load cell, is an instrument that is commonly affixed to the vehicle’s various components — including the rod end, suspension pushrods, gear lever, steering column, driveshaft, pedals and more. These instruments can then measure the wheel load, for example, as a car hugs a tight turn in real time. The in-vehicle data logger picks up every load change caused by high-speed acceleration, breaking and maneuvering.
Ultimately, load cells and strain gauges are an irreplaceable tool for anyone looking to push the limits and fully understand racecar performance.
Our engineers have installed load cells and strain gauges on structures and machinery around the globe for decades. We take pride in perfecting the art of strain gauge application, logging, measurement and analysis — whether on vehicles, medical devices or rocket components.
We are also confident in our custom iTestSystem software, which allows us to stream and analyze load cells, strain signals and do real world fatigue data acquisition. Contact our strain lab and technicians to build a custom real time strain monitoring system or to design, build, calibrate and test strain-based load cells.
Contact us for more information about our automotive, strain gauging and testing services.