Tag Archive for: strain gauge
Strain Gauge Rosette Analysis
in Aerospace | Defense, Automotive, Blog Posts, Civil | Infrastructure, Energy, Off-Highway, Power Generation, Pulp & Paper, Video/by Mark YeagerHow to Validate your next Finite Element Analysis (FEA) Model using Strain Gauges
in Aerospace | Defense, Automotive, Blog Posts, Civil | Infrastructure, Off-Highway/by Mark YeagerStrain Gauges Improve Cooling Tower Fan Performance
in Blog Posts, Civil | Infrastructure, Energy, Power Generation, Pulp & Paper, Strain Gauge Services/by Mark YeagerITM Engineers Strain Gauge in Shadow of Artemis I Rocket Launch
in Aerospace | Defense, Blog Posts, Engineering Services Posts, Strain Gauge Services/by Mark Yeagerï»ż
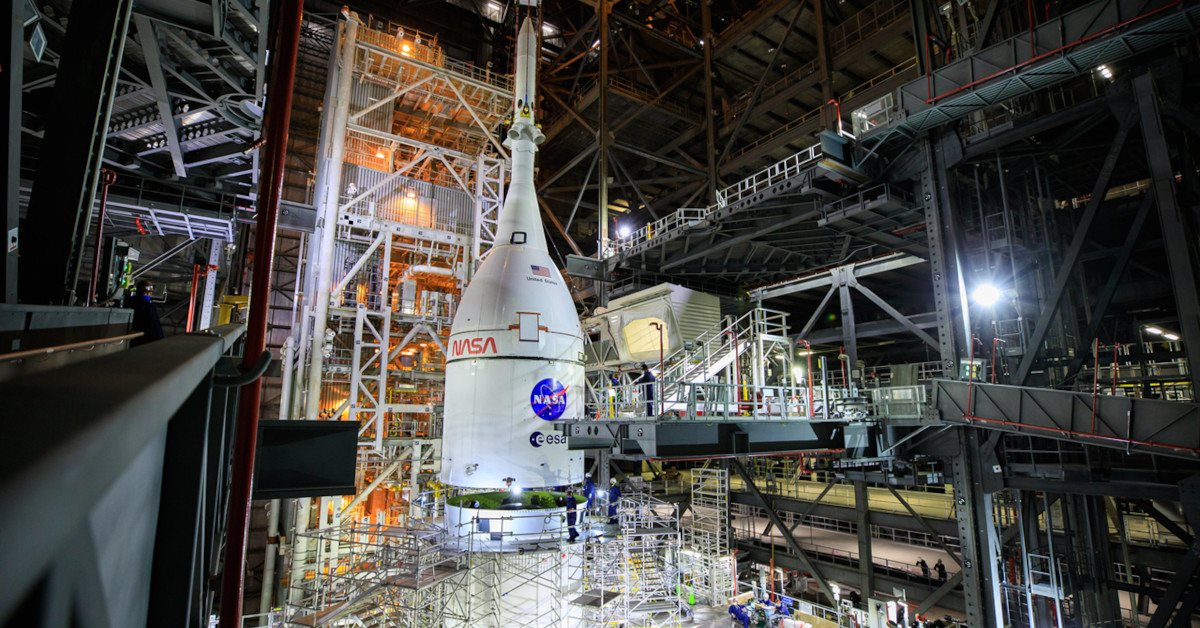
Engineers Test Artemis I Spacecraft Orion at Johnson Space Center
ITM strain gauge team witnesses powerful forces during two-week trip to Cape Canaveral
A group of engineers and aerospace engineering technicians from Integrated Test & Measurement just returned after an unforgettable experience in Cape Canaveral.
ITMâs team was there to assist an aerospace engineering partner with on-site strain gauging. The challenge was to assist in validating rocket components ahead of an upcoming launch, which required completing a massive strain gauge instrumentation project.
ITMâs team was there to assist an aerospace engineering partner with on-site strain gauging. The challenge was to assist in validating rocket components ahead of an upcoming launch, which required completing a massive strain gauge instrumentation project.
The teamâs work was delayed due to Hurricane Nicole, so they waited out the storm just blocks from the beach, said Ryan âRJâ Matthews, ITM engineer. As powerful as it was seeing a storm with wind speeds exceeding 130 mph, the hurricane was still a distant second in the most memorable department to their up-close view of NASAâs Artemis I mission rocket launch.
Matthews said the team took a break from strain gauging a rocket booster, an intense project that required a significant amount of cable routing, to observe the launch from just a few miles away.
To accommodate their partner, ITMâs crew worked eight 12-hour shifts from 5 p.m. to 5 a.m., so perfect timing to watch NASA take a first step toward blazing a path back to the Moon in the early hours of Nov. 16.
About 45 minutes after the anticipated launch time, fireball from the SLS Rocket lit up the night sky.
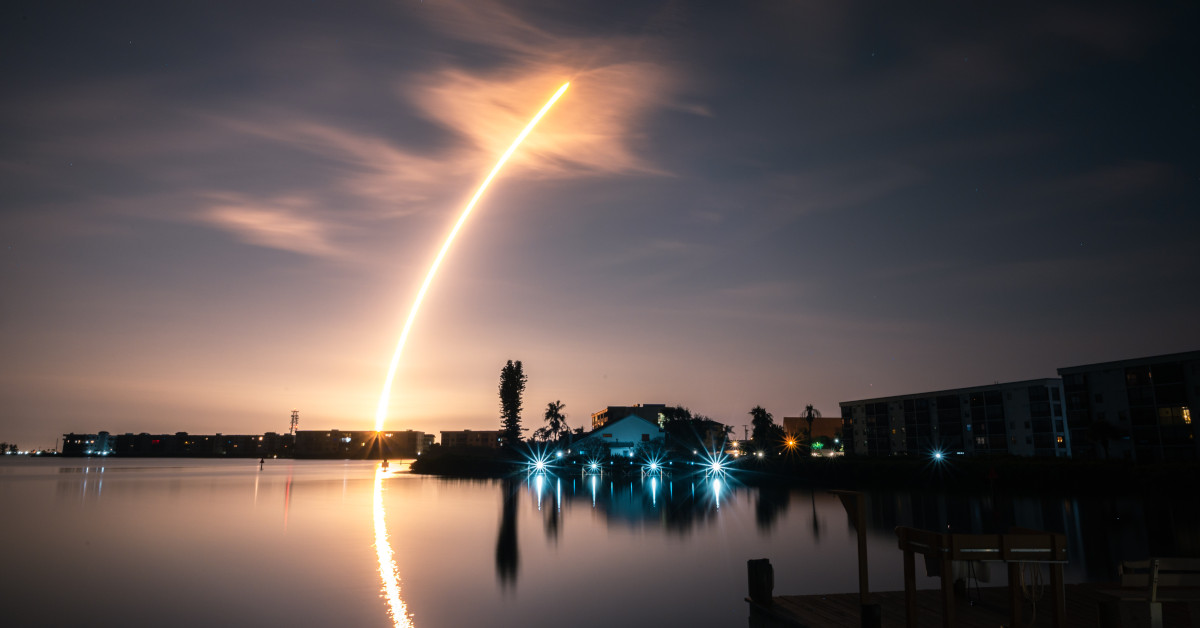
Artemis I SLS Rocket Launch Time Lapse
âIt was incredible,â said Matthews, who witnessed the launch from a balcony. âIt was super bright â kind of like a 1-minute sunrise. About 40 seconds later, it started rattling the building.â
Contact us for more information about our aerospace, strain gauging and testing services.
Endless Testing Options Through Finite Element Analysis (FEA)Â
in Aerospace | Defense, Automotive, Blog Posts, Civil | Infrastructure, Construction | Mining, Energy, Off-Highway, Power Generation, Pulp & Paper/by Ryan Welkerï»ż
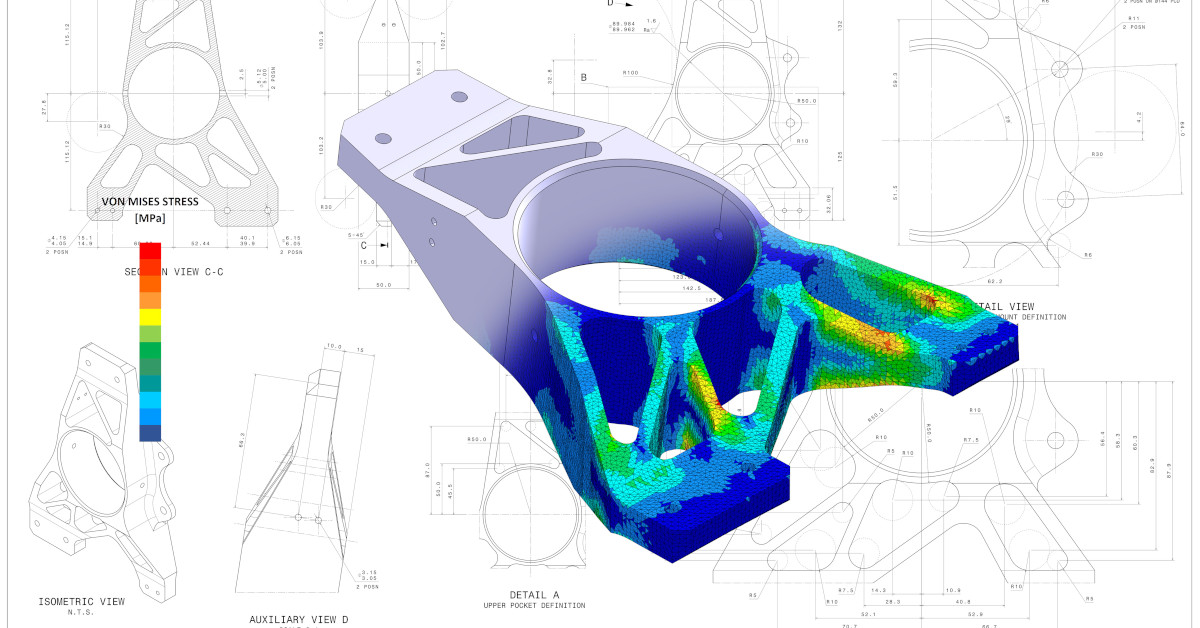
Design Validation Finite Element Analysis (FEA) using strain gauge measurements.
Endless Testing Options Through Finite Element Analysis (FEA)Â
Whether our customers need us to validate their Finite Element Analysis (FEA) models or perform both the physical testing and the FEA, our engineers are used to helping customers with complex testing and analysis of high-value equipment.Â
As a recent example, our team is involved in a large-scale project to do engine testing for a client that requires ITM to do both the physical testing as well as the FEA simulations. This requires using a custom high-channel count telemetry system to transmit engine data to a receiver that is sampling at an extremely high rate.Â
âOnce you are able to bring in the test data and compare it to the simulated data, you are able to fine tune your FEA simulation to better reflect the real-world application,â said ITM engineer Ryan Matthews. âWe can also simulate the test in software and predict how it is going to react to the test when we can actually measure such things as strain, stress and vibration.âÂ
Matthews points out that FEA technology also helps the team determine the precise best placement of strain gauge during physical testing. And depending on complexity, a single simulation can take a few seconds or months to run.Â
For obvious reasons â mainly the cost of bringing high-value assets to failure â running repeated strain gauge tests on components simply isnât feasible, but ITMâs in-house capabilities and close partnership with sister firm SixDOF opens up endless FEA simulation options to clients.Â
âSometimes you are only going to be able to test a structure or a part once before it fails,â says Matthews. âSo it becomes crucial to do a limited number of physical tests then correlate that to your FEA. Then you can pretty much run unlimited simulations.âÂ
For more information about our testing, strain gauging, and FEA modeling services contact Ryan Welker via email at ryan.welker@itestsystem.com of phone @ (844) 837-8797.
Engineering Data Acquisition Tools: NI-9237 Bridge Input Module
in Blog Posts, Strain Gauge Services/by Ryan Welkerï»żï»ż
For bridge type sensors and most strain gauges configurations (full and half bridges), our engineers will opt for the NI-9237 C-Series module to acquire strain and bridge data instead of the NI-9235 or NI-9236 modules. Â Unlike the NI-9236 module, the NI-9237 can acquire data from:
- Any resistance strain gauge (not just 120 or 350 Ohm)
- Quarter, half, and full-bridge strain gauge configurations
- Torque and load cells (off-the-shelf and custom)
The NI-9237 is a 4-Channel C Series strain/bridge input module that contains circuitry to power, scale and calibrate strain and load sensors . For quarter and some half bridge measurements a bridge completion module must be used in conjunction with this module. The NI-9237 module provides internal bridge excitation (2.5V, 3.3V, 5V, or 10V) and shunt calibration resistors for sensor scaling verification. To collect synchronized and scaled high-speed (50kHz) structure strain and load cell data, use our iTestSystem engineering measurement software.
For more information about the NI-9237, DAQ module rental, strain gauge installations or our data logging solution iTestSystem, contact Ryan Welker via email: ryan.welker@itestsystem.com or phone: (844) 837-8797 x706.
Strain Gauge Installation – M-Bond AE-10 Epoxy
in Aerospace | Defense, Automotive, Blog Posts, Civil | Infrastructure, Construction | Mining, Off-Highway, Power Generation, Pulp & Paper/by Mark YeagerThis video shows how to install a strain gauge on a curved surface using M-Bond AE-10 two part epoxy. Watch an ITM test technician walk through each step of the M-Bond AE-10 strain gauge installation procedure.
ITM Going to New Heights with Aerospace Clients
in Aerospace | Defense, Blog Posts/by Tim Carlier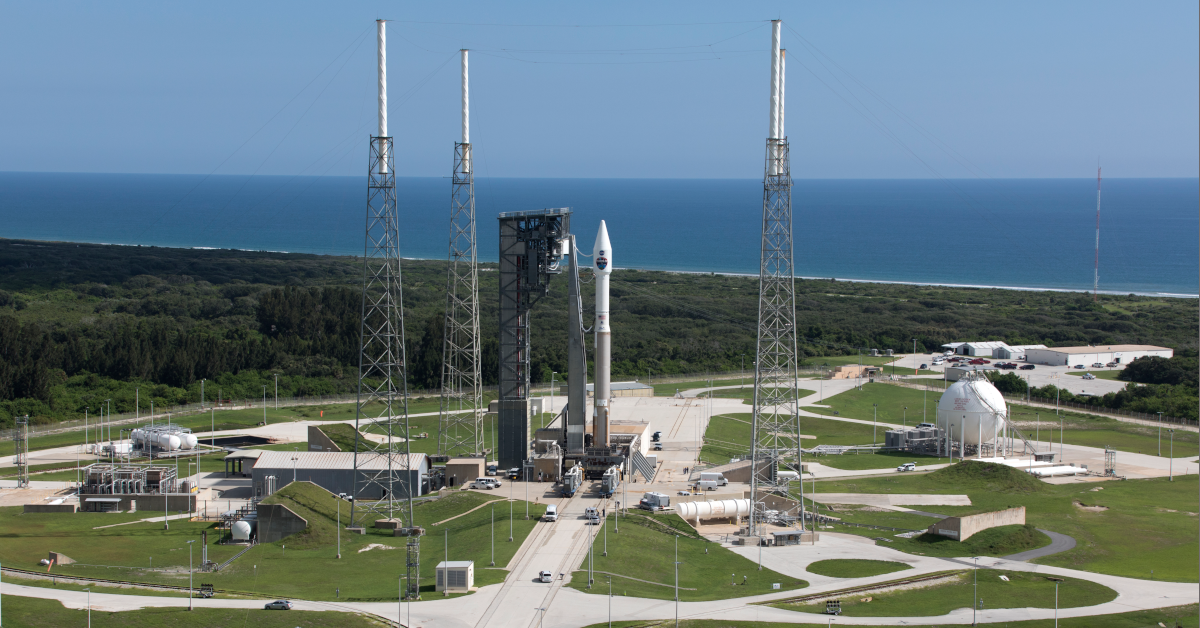
A commercial airliner touches down and brakes safely so hundreds of passengers can exit at their destination. A solid rocket booster separates from a space flight as the main payload overcomes gravity to head into orbit. A military drone completes its mission over enemy territory.Â
In a very real way, the team of engineers at Integrated Test and Measurement (ITM) goes along for the ride during plenty of crucial moments in the aerospace realm. From doing data collection to measure the stress load of an airplaneâs landing gear to installing strain gauges on rocket components to gather more than a thousand channels of data, ITMâs testing and measurement services are going to incredible heights. Â
Ryan Welker, ITM vice president of operations, says their aerospace partners most often turn to the Milford, Ohio, engineering service and software company for their expertise in testing and design validation, particularly if the project involves complex strain gauge work.Â
âA lot of times when you are dealing with aerospace requirements, it involves challenging materials. You arenât just working with steel, and itâs quite a bit different installing strain gauges on titanium or carbon fiber. It makes the installation process a little more challenging, but weâve been taking tough measurements in extreme environments around the globe for 20-plus years. Our experience in strain gauging is more of an art than a science.âÂ
Welker points out that ITM wonât hesitate to put boots on the ground for their aerospace partners who have complex challenges. That was the case when a high-end aerospace company rang him up in desperate need of structural testing on a crucial component ahead of a launch. Though the job would require several people on-site for multiple months, Welker and team made it work. They installed strain gauges around the clock for three months so their client could complete crucial validation testing on a design. ITM delivered, and the client made their deadline.Â
Often during these intricate instrumentation processes, the ITM team employs the capabilities of their custom iTestSystem software to monitor stresses during complex assemblies. Aerospace companies may also rent ITMâs custom-built acquisition hardware to record data, even if it means that ITM needs to conduct onsite demonstration, support or help with analysis.Â
âWe donât just offer the ability to run a test,â says Welker. âWe train your folks to use it.âÂ
In the end, ITM offers innovative test solutions and a range of aerospace testing services designed to help the industry develop superior products and processes. Â
Key Services for Aerospace ClientsÂ
Strain Gauge InstallationÂ
Installing strain gauges in the field for structural and fatigue measurements requires expertise and experience. Our field service technicians and engineers have installed strain gauges on structures and machinery around the globe for decades. Whether you use our iTestSystem software to stream and analyze strain signals for static measurements and real-world fatigue data acquisition, or contract our software engineers to build a real-time strain monitoring system, we will make sure you acquire quality strain data for your aerospace project.Â
Structural and Mechanical TestingÂ
Our team of engineers have decades of experience in performing structural testing in aerospace and many other markets. Testing services include Impact Testing and Modal Analysis, Structural Dynamics Operating Tests, Data Logging and Unattended Data Acquisition.Â
Our engineers can assist you with any part of the testing process. This includes test planning, onsite sensor installation and data acquisition and remote test monitoring.Â
High Channel Count Structural DAQ SystemsÂ
In our work, we often collect strain, vibration, voltage, and other signals simultaneously that require well over a thousand total sensor channels. Network synchronization technology embedded within the NI cDAQ chassis allows users to account for the sheer number of channels during these structural tests. The true secret to our success in these high-channel jobs has been our iTestSystem software which leverages the cDAQâs synchronization technology while providing an intuitive data acquisition and sensor configuration and setup.Â
Rugged Data Acquisition Systems for RentÂ
If the right tool doesnât exist, build it. For years that has been the approach ITM engineers have taken when it comes to gathering data and building tests for clients. And after decades of performing structural testing in aerospace, off-highway, automotive, industrial and many other environments, weâve built up an impressive line of custom Rugged Data Acquisition (RAC) Systems which will perform under harsh testing conditions.
For more information about our DAQ Rental Hardware, data collection or Testing Services, contact Ryan Welker via email at ryan.welker@itestsystem.com.
Railcar Structural Testing Case Study
in Automotive, Blog Posts, Case Study, Civil | Infrastructure, Off-Highway/by Ryan WelkerObvious signs of fatigue â cracks at the corners of doors â had begun to surface on an in-service Railcar. A railcar structural testing case study.
CONTACT INFORMATION
ITM | Integrated Test + Measurement
227 Water Street, Suite 300
Milford, OH 45150
Phone: 1.844.TestSys
Fax: 513.248.8453
Email: ITM Sales
ITM provides software development, structural and mechanical testing services, industrial monitoring, strain gauging, and data analysis solutions to clients on six continents. ITM is a recognized National Instruments Gold Alliance Partner.